1.Pulp Moulding production line is known as egg tray line for using massively in produce egg tray.
2.Pulp Moulding production line, which uses waste paper, cardboard, leftover material of paper mill, by hydraulic pulper, mix making a certain dense pulp, and pulp is absorbed by vacuum of special metal moulding to become wet products, through drying , and shaping to become finished products.
3.Pulp Moulding Line processing makes use of recycled water and does not lead to water or air pollution. Finished packaging products can be recycled after being used in storage, transport, and sales. After shredding, they are easy to be decomposed as paper, even if discarded into the natural environment.
4.Automatic pulp molding production lines can be mass production of various food container, egg tray, lunch boxes and so on.
Machine Model
|
1*3/1*4
|
3*4/4*4
|
4*8/5*8
|
5*12/6*8
|
Yield(p/h)
|
1000-1500
|
2500-3000
|
4000-6000
|
6000-7000
|
Waste Paper(kg/h)
|
80-120
|
160-240
|
320-400
|
480-560
|
Water(kg/h)
|
160-240
|
320-480
|
600-750
|
900-1050
|
Electricity(kw/h)
|
36-37
|
58-78
|
80-85
|
90-100
|
Workshop Area
|
45-80
|
80-100
|
100-140
|
180-250
|
Drying Area
|
No need
|
216
|
216-238
|
260-300
|
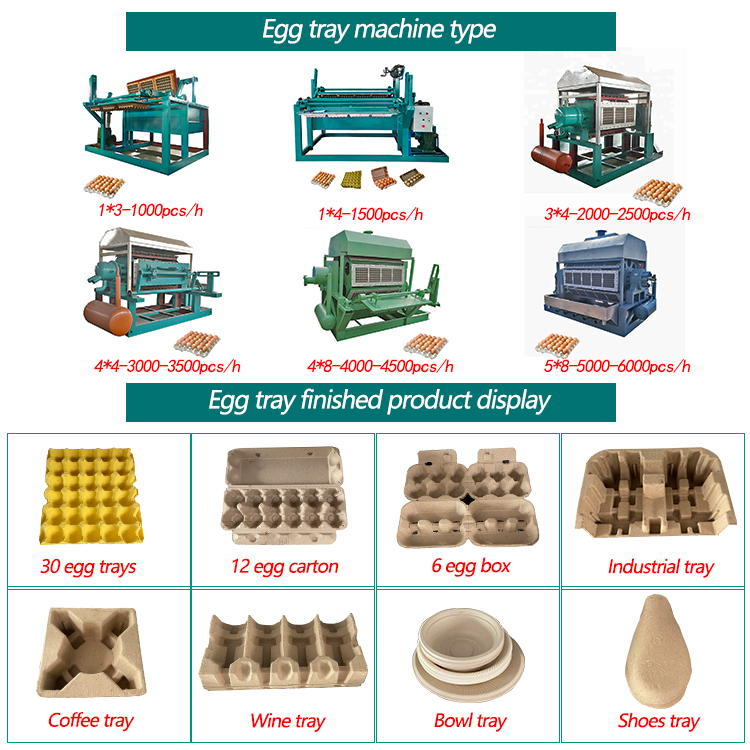
High precision servo motor drive,high efficiency and energy-saving drying line.
1,Use precision reducer servo motor forming and transferring to ensure smiith and fast operation.
2,Use absolute encoder to achieve accurate correction.
3,The use of bronze casting static and dynamic ring structure is more suitable for product dewatering process.
4,The use of mechanical structure to ensure that the mold close on both sides evenly.
5,Large capacity; Water content is low;Save the cost of drying.
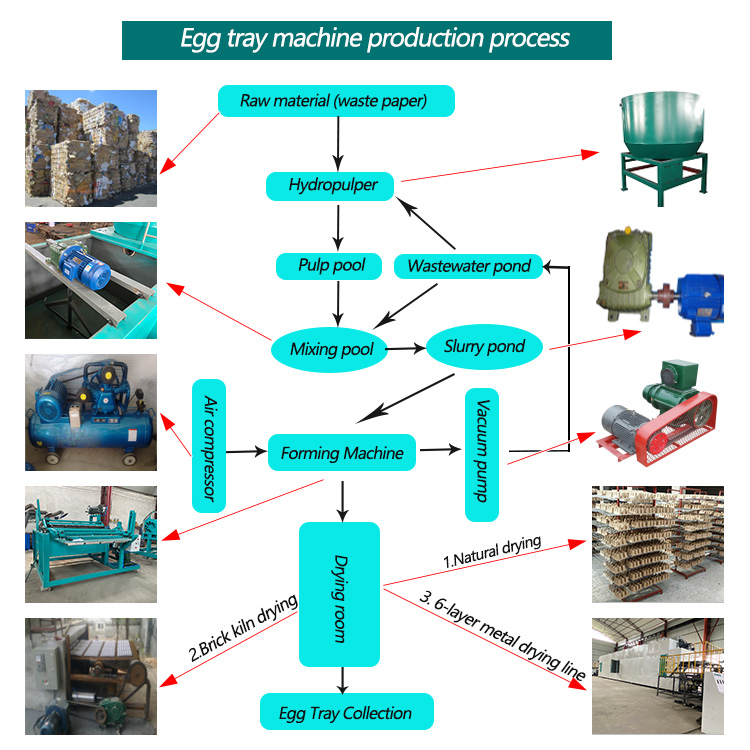
1.Pulping system
2. Forming system
3. Drying system
(3) New multi-layer drying line: 6-layer metal drying line can save more than 30% energy
4. Finished product auxiliary packaging
(2) Baler
(3) Transfer conveyor
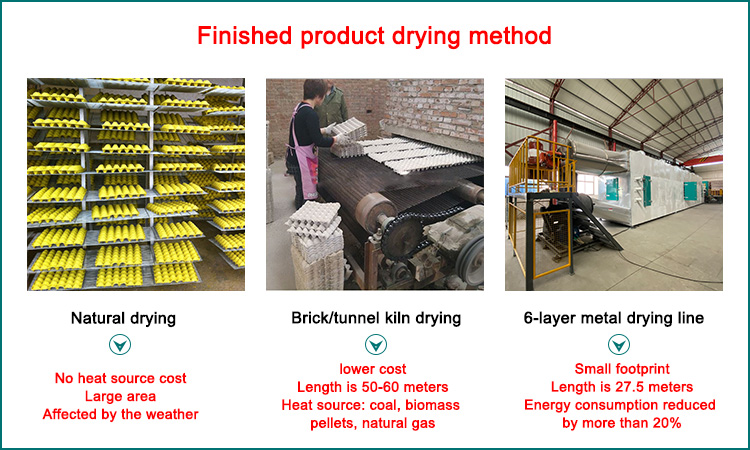
-
Automatic waste paper pulp egg tray making mach...
-
YB-1*3 egg tray making machine 1000pcs/h for bu...
-
Egg Tray Pulp Molding Making Machine for Small ...
-
Young Bamboo paper egg tray making machine auto...
-
Automatic paper pulp egg tray production line /...
-
1*4 waste Paper Pulp Molding Drying Egg Tray Ma...